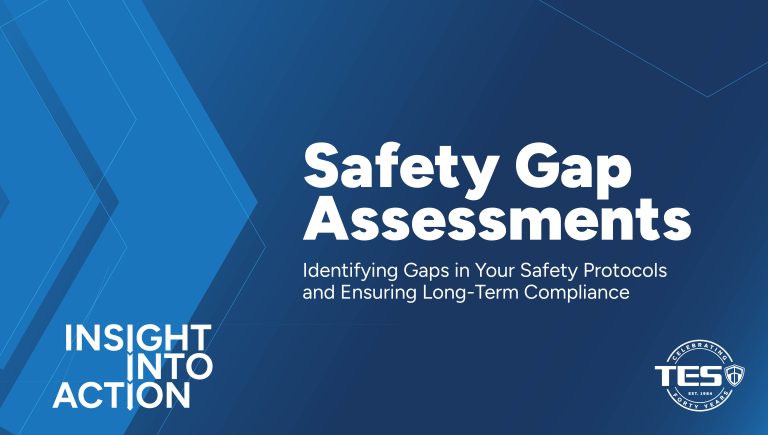
Safety Gap Assessment
April 1st 2025
A Safety Gap Assessment is a powerful tool for ensuring your organization’s safety protocols are effective and compliant with the latest regulations. This detailed audit identifies any gaps in your current safety measures, helping you stay ahead of potential risks. But how does this differ from a risk assessment, and why is it so important? Let’s break it down.
This assessment is a comprehensive audit that evaluates your organization’s existing safety policies, procedures, and systems. The goal is to identify any areas where current practices fall short of safety standards or regulatory requirements. These gaps could range from outdated safety policies to insufficient emergency preparedness protocols. Once these gaps are identified, actionable steps are provided to close them, ensuring your company stays compliant and minimizes risks.
Safety Gap Assessment vs. Risk Assessment: What’s the Difference?
At first glance, you might think a Safety Gap Assessment sounds similar to a Risk Assessment, but they serve distinct purposes:
- Risk Assessment: Focuses on identifying potential hazards in the workplace and evaluating the risk associated with those hazards. This is usually the first step in implementing safety controls.
- Safety Gap Assessment: Focuses on evaluating the effectiveness of the safety controls already in place. It looks at the bigger picture to ensure that your systems and policies are up to date and fully compliant with current regulations.
In short, a risk assessment identifies what could go wrong, while a gap assessment identifies what isn’t working as expected in your existing safety measures.
What’s Included?
A typical assessment is a thorough review that may include the following steps:
Evaluation of Current Safety Policies: Analysis of existing safety procedures to ensure they meet industry standards.
Regulatory Compliance Review: Verification of compliance with OSHA and other relevant safety regulations to identify any non-compliance risks.
Organizational Involvement: Collaboration with safety officers, management, and employees to gather a complete understanding of the current safety landscape.
Identification of Gaps: Pinpointing where safety practices fall short—whether due to outdated equipment, incomplete procedures, or untrained staff.
Recommendations for Improvement: Clear, actionable steps to close identified gaps and ensure compliance.
It’s important to note that these are common steps in a gap assessment, but the exact process can vary. To get a precise and tailored assessment, it’s best to consult with a safety expert who can evaluate your organization’s specific needs and challenges.